
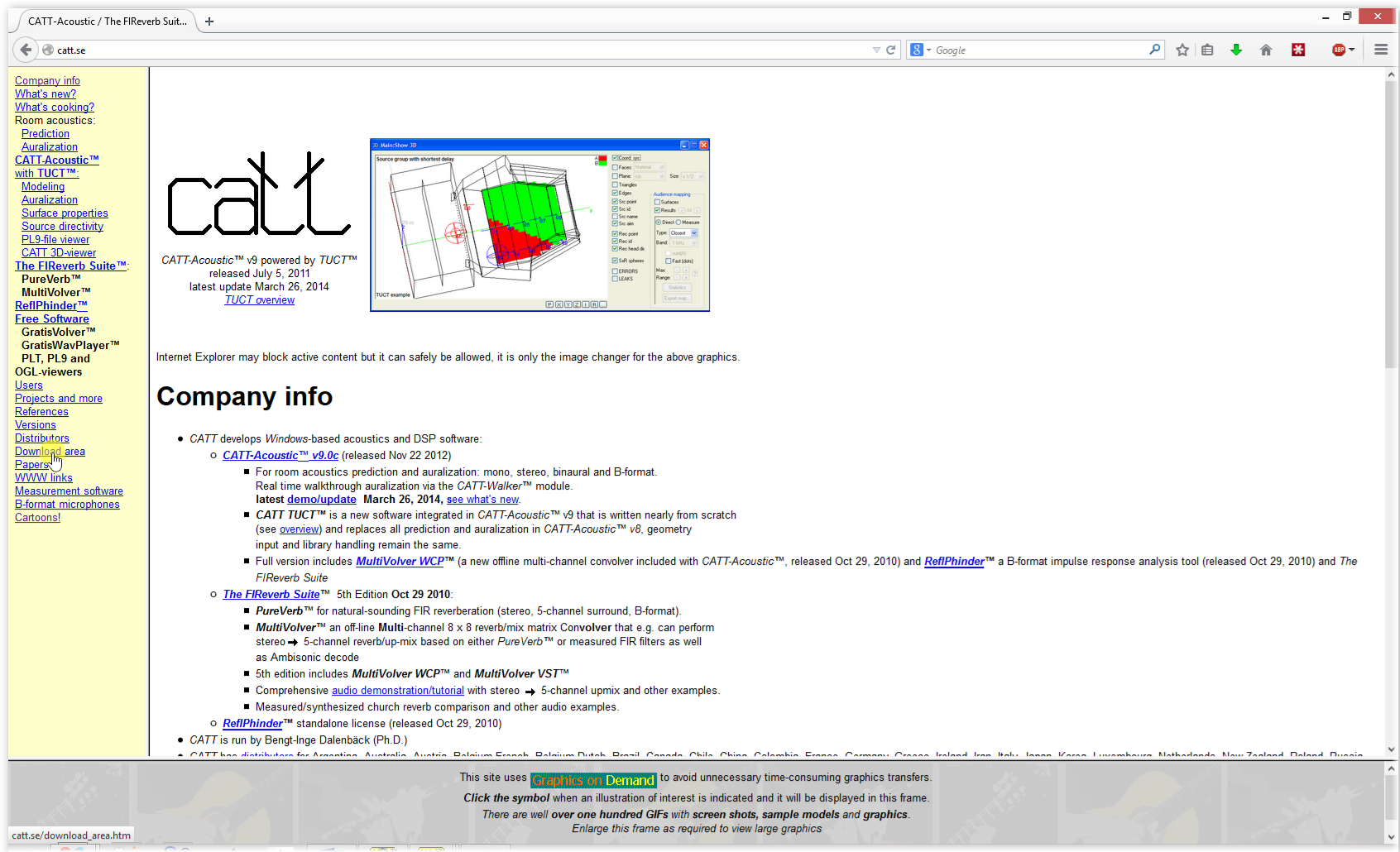
These are outside the scope of clean room basics, reading this blog on could assist. Unlike powders, droplets of liquid don’t generally “leap up” and float around the facility.Designs can become complicated if the products or raw materials are highly potent, which cause occupational health and safety issues, or if there is a need for biological containment. So these facilities are normally designed with “dirty corridors” as you want to keep potential microorganisms out of the cleanroom. This means that the rooms are negatively pressurised to the corridor.For aseptic (processed), sterile, or low bio-burden and liquid medicinal products, the opportunistic microorganisms usually will find supportive media in which to flourish, or in the case of an aseptically processed product, a single microorganism could be catastrophic. “Clean corridor” or a “Dirty corridor”?When considering pressures cascades, the pharmaceutical engineers should consider a design philosophy to have a “clean corridor” or a “dirty corridor” design, which we will now explain through an example.
#Catt acoustic v8 iso#
Usually manufacturers will define an airborne particulate concentration standard class such as ISO 8 (at rest), outline gowning and a pressure cascade regime, defining a “clean corridor” design or a “dirty corridor” design.If you are a manufacturer of sterile medicinal products, you must follow the EU or PIC/S GMPs, namely Annex 1. What type of clean room do I need?If you are a manufacturer of non-sterile medicinal products, you should define your own clean room / area standards using national and international standards. If you have classified the room as Grade D, you will need to live with the consequences and costs of maintaining this level of clean room cleanliness during operation.
#Catt acoustic v8 code#
Whilst not a code requirement, many regulators, like the Australian TGA will expect you to fully comply with all of the requirements for a Grade D room as defined in Annex 1, even if it’s not a GMP code requirement. This Annex defines a number of additional requirements besides the airborne particulate concentration limits used to classify clean rooms.In a nutshell, if you manufacture a non-sterile medicinal product, you should be very careful about classifying or grading your clean areas, for example, classifying a room as “Grade D”. On the other hand, for the manufacture of sterile medicinal products, clean rooms are mandatory, as defined in Annex 1 of the EU and PIC/S GMPs. TGA) GMP guidance’s for the manufacture of non-sterile medicinal products in a “clean room”, but we do use clean areas that are effectively ventilated with filtered air where the products or open clean containers are exposed.
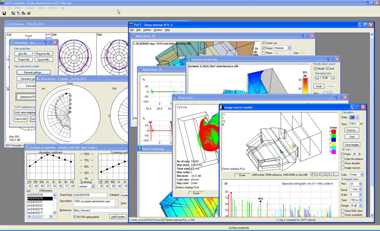
So why do I need a clean room?There is no GMP requirement in the EU and PIC/S (i.e. Annex 1 of both the and Guides to GMP and other standards and guidance as required by local health authorities. In a pharmaceutical sense, clean rooms are those rooms that meet the code of GMP requirements as defined in the sterile code of GMP, i.e. If there are significant containment requirements, the requirements would be outside the scope of a “simplistic” blog like this. In this blog I will attempt to explain the necessary characteristics of a regulated company clean room not producing potent chemicals or active or hazardous biologicals.

Basic Clean Room Requirements Designs for GMP Clean Rooms What is a clean room?A clean room (GMP cleanroom), in my mind are a combination of engineering design, fabrication, finish and operational controls (control strategy) that are required to convert a “normal” room to a “clean room”.
